Every company wants to produce a good quality product. In some industries this is more important than in others. In highly regulated industries where precision and compliance is not only important but regulated, quality assurance takes on an even greater level of importance. Quality assurance is how companies ensure there are no defects or mistakes made when they manufacture a product. The term is often used interchangeably with quality management or quality control but this is a smaller, specific part of these larger, holistic product management programs.
Companies have many choices in quality assurance approaches. Mostly, which approach or approaches a company uses depends on what the company produces and what level of quality they are trying to ensure. A food company will use a different approach than a software company, which will use a different approach from a precision manufacturing company in an industry like the aerospace industry. Here is a look at four quality assurance approaches for different types of businesses.
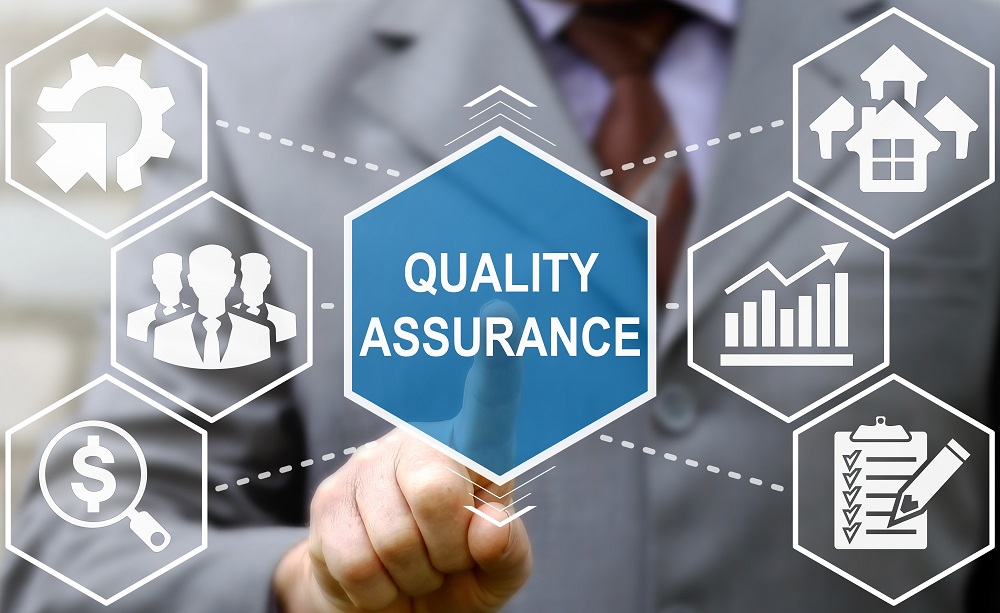
1. HACCP
Hazard analysis and critical control points (HACCP) is a quality assurance approach you will most often see in the food industry. However, this method is now being used more often in industries such as pharma and cosmetics. Food scientist Dr. Howard Eugene Bauman originally created it to keep food safe for astronauts in the 1960s but it has since become the FDA standard used to keep all Americans’ food safe.
HACCP works through company implementation of a quality assurance plan that limits products’ exposure to possible contaminants. This is easier, safer and more efficient than having to test all finished products for safety or contaminants. The point of this process is to keep food (or other products) safe for use; it does not necessarily ensure the overall quality of the products.
This process consists of seven principles companies employ to keep products safe. These principles are:
- Hazard analysis
- CCP identification
- Establishing critical limits
- Monitoring procedures
- Corrective actions
- Verification procedures
- Record-keeping and documentation
Following these seven principles should allow companies to minimize exposure to contaminants by monitoring, correcting, and verifying data at each step (or “critical point”) in the manufacturing or transportation process. When done correctly, this quality assurance process has been shown to keep products safer for consumers.
2. IQ OQ PQ
This qualification process is used for machinery and equipment to ensure that companies produce products of a precise quality level. It is found in several highly-regulated industries such as aerospace, medical device manufacturing, pharmaceuticals, and other highly specialized industries producing delicate products. It is a three-step process that involves installation qualification (IQ), operational qualification (OQ), and performance qualification (PQ).
These three types of qualifications are conducted in order to ensure that machinery or equipment is able to produce consistent, good quality results. The process begins with IQ which starts when the company first acquires a machine. IQ checks that it is the correct machine and that it is set up to the specifications they need.
After that, OQ is performed. This is where a machine is run under simulated conditions to make sure it can perform and deliver the required results. The third step is PQ when the machine is fully integrated into the process. Before it starts running for real, though, extreme conditions are simulated to create boundaries that will help operators know the exact capabilities of the machinery.
With this quality assurance process, precision manufacturing industries are able to make sure that their machinery works in every way they need before it ever starts manufacturing a product that will go to a consumer. Dickson’s guide to IQ OQ PQ is a helpful resource if you want to explore the topic in more depth.
3. Data Conversion Testing
In the software industry, data conversion testing is a very important approach to quality assurance. Data conversion is often confused or used interchangeably with data mitigation but they are two different things. Data mitigation refers to moving data from one system to another. Data conversion is about transforming data from one format to another. Depending on the systems, in order to perform data mitigation you may have to first carry out data conversion. Data conversion testing becomes especially important when performing data mitigation.
Conversion testing is conducted when data need to be transformed to work with a different program than the one in which it currently exists. This can happen when data stored on your system needs to be used with a web-based application or when you are moving from legacy software to a new system. This testing will help ensure that the data will accurately transfer formats so it can be used to produce the insights you need and that data won’t be lost or destroyed in the process.
4. Benchmarking
This is a quality assurance approach used in highly competitive industries such as consumer product manufacturing. The idea behind benchmarking is for a company to use statistical data to identify pain points and strengths. This is accomplished by comparing your own products and processes against those of your competitors. This will show you where you stand in the industry and the areas that need to be improved. Benchmarking can also be used to compare your own historical data to current data to help establish improvement metrics.
The benchmarking process includes many steps, but the basic idea can be boiled down to just a few. First, you need to collect data about your own processes and results and then about the processes and results of the leaders in the industry. When that is done, you can establish benchmarks to achieve in order to catch, and ultimately pass, these leaders. When you have the benchmarks, you can make continuous improvements and analyze your success and failures along the way to speed up the process.
Benchmarking is a great quality assurance practice to implement if you want to make fast, efficient improvements to become a leader in a competitive industry. It needs much research, data, and analytics but once you have the benchmarks in place, the improvement part becomes much easier.
Conclusion
While these four quality assurance approaches are widely used in specific industries, they can also be applied in others. Any industry in which safety and quality matters may be able to benefit from an approach used in another industry with the same concerns. Knowing about these approaches could help your company improve and produce better products, a good goal for any industry.
Add Comment